Table of Contents
ToggleIntroduction
RFID (Radio Frequency Identification) labels are crucial in various industries for tracking and managing assets, inventory, and information. These labels integrate RFID technology into a compact, versatile format that can be adhered to items for seamless identification and data collection. Creating RFID labels involves several steps, from choosing suitable components to programming and testing. This guide will walk you through the process of making RFID labels to ensure they meet your specific application needs.
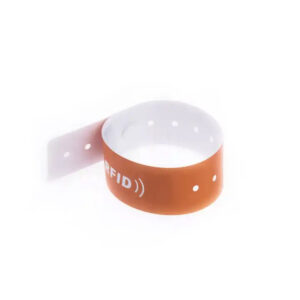
Choosing the Right Components
Selecting the RFID Chip
The RFID chip is the heart of the RFID label, responsible for storing and transmitting data. When selecting an RFID chip, consider its frequency (LF, HF, or UHF), memory capacity, and read/write capabilities. Low-frequency (LF) chips are ideal for applications like animal tracking, high-frequency (HF) chips are commonly used in access control and payment systems, while ultra-high-frequency (UHF) chips are perfect for logistics and supply chain management.
- Key Points:
- Choose based on frequency: LF, HF, or UHF.
- Assess memory capacity needs.
- Determine read/write capabilities.
Selecting the Antenna
The antenna in an RFID label is vital for communication between the RFID chip and the reader. The type and design of the antenna affect the range and reliability of data transmission. Copper and aluminum are common materials used in RFID antennas. Ensure the antenna is compatible with your selected RFID chip and is designed to meet the requirements of your specific application, whether it’s for short-range personal identification or long-range inventory tracking.
- Key Points:
- Consider material: copper or aluminum.
- Ensure compatibility with RFID chip.
- Match the antenna design to application needs.
Designing the RFID Label
Label Substrate and Printing
The substrate is the material on which the RFID chip and antenna are placed. Common substrates include paper, plastic, and polyester, chosen based on the intended environment and durability needs. The printing process involves adding information and designs to the label, such as logos, barcodes, and product details. High-quality printing ensures the label is both readable and professional.
- Key Points:
- Choose a durable substrate: paper, plastic, or polyester.
- Ensure printing quality for readability and professionalism.
- Include essential information and designs.
Label Size and Shape
The size and shape of an RFID label are determined by the item it will be adhered to and the application’s specific requirements. Labels can range from small, discrete tags to larger labels for pallets and containers. Custom shapes can be designed to fit particular items, enhancing the label’s effectiveness and ensuring it does not interfere with the item’s appearance or functionality.
- Key Points:
- Adjust size and shape to fit the item.
- Design for unobtrusive placement.
- Consider application-specific requirements.
Programming and Encoding the Labels
Writing Data to the RFID Chip
Once the RFID label is physically assembled, the next step is to program the RFID chip with relevant data. This process involves writing unique identifiers or data sets onto the chip using an RFID writer. It’s essential to ensure accuracy in the data encoding process to prevent errors in tracking and identification.
- Key Points:
- Use an RFID writer for data encoding.
- Ensure data accuracy and uniqueness.
- Prevent errors in data management.
Security Features
Encoding security features into the RFID chip is crucial for preventing unauthorized access and data tampering. Implement encryption algorithms and password protection where necessary to safeguard the information stored on the RFID label. These security measures help maintain the integrity and confidentiality of the data.
- Key Points:
- Implement encryption for data protection.
- Use password protection for enhanced security.
- Safeguard data integrity and confidentiality.
Testing and Quality Assurance
Functional Testing
Before deploying RFID labels, perform functional tests to ensure they operate correctly under real-world conditions. Functional testing involves verifying the label’s readability at various distances, angles, and environments. Ensure that the labels meet the operational criteria for your specific application, ensuring reliability and effectiveness in actual use cases.
- Key Points:
- Test readability in different conditions.
- Verify operational effectiveness.
- Ensure compliance with application requirements.
Durability Testing
RFID labels must withstand the environmental conditions they will encounter during use. Conduct durability tests to assess the label’s resistance to physical wear, moisture, temperature changes, and chemical exposure. These tests help ensure that the RFID labels remain functional and legible throughout their lifespan, regardless of the conditions they face.
- Key Points:
- Assess resistance to environmental stress.
- Ensure longevity and functionality.
- Test against application-specific conditions.
Conclusion
Creating RFID labels involves a detailed process of selecting the right components, designing the label, programming the chip, and thorough testing. Each step is crucial to ensure the final product meets the desired standards of functionality, durability, and security. By following these guidelines, you can produce reliable RFID labels tailored to your specific needs, enhancing efficiency and accuracy in tracking and managing items across various applications. The meticulous creation and testing of RFID labels ensure that they serve their purpose effectively, providing seamless and secure data communication in a wide range of environments.